The marine environment is a complex corrosive environment. In this environment, corrosive substances such as acids, alkalis, and salts in seawater will cause serious erosion to equipment in marine engineering. As an economical and practical steel, spring steel is widely used in marine engineering. In order to ensure the reliability of the equipment, the spring steel used in the marine environment must take some anti-corrosion measures. Today we will introduce in detail the anti-corrosion measures for spring steel in marine environment.
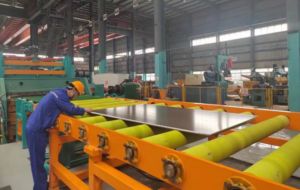
Anti-corrosion Measures for Spring Steel in Marine Environment:
First, material selection. Since spring steel contains a lot of iron elements, it is very easy to rust in the marine environment, and long-term use will affect the service life of engineering equipment. Therefore, in marine engineering, choosing spring steel with good corrosion resistance can reduce the workload of maintenance.
Secondly, coating protection. Galvanizing or cadmium plating on spring steel can form a dense protective layer on the surface of the spring steel, which can effectively prevent corrosion caused by seawater. For example, cadmium plating has high corrosion resistance. Cadmium plating on spring steel is not only beautiful, but also enhances the protective effect.
Furthermore, coating protection. Spray high-performance anti-corrosion coatings on the surface of spring steel, such as epoxy paint, chlorinated rubber paint, polyurethane paint, etc. A continuous and dense protective film can be formed on the spring surface to prevent seawater, oxygen and other corrosive substances from contacting the spring steel surface and ensure the stability of the equipment structure.
In addition, vapor phase rust prevention. During the gas-phase anti-rust treatment of spring steel, because the gas-phase corrosion inhibitor can continue to vaporize and volatilize slowly at room temperature, the volatilized corrosion inhibitor gas is adsorbed on the exposed metal surface and can form a stable protective film. This can crowd out the gaseous water molecules on the surface of the spring, preventing condensation from forming and causing corrosion.
In addition, environmental control. The rusting speed of spring steel is closely related to the ambient humidity. Therefore, during use, the exposure time of the spring in high humidity and high salinity environments should be minimized. Especially in special use environments, environmental control, such as ventilation, dehumidification, etc., must be carried out.
Finally, maintenance. During use, the spring steel should be inspected regularly to detect and deal with signs of surface corrosion in a timely manner. If abnormal conditions such as rust are found, repair or protective treatment should be carried out in time to extend the service life of the spring steel.
Conclusion
In short, spring steel is extremely prone to chemical reactions with oxygen in the air due to its material composition. Taking the above various anti-corrosion measures can effectively improve the corrosion resistance of spring steel in the marine environment and extend the service life of the spring. In practical applications, appropriate anti-corrosion measures need to be selected based on factors such as the specific use conditions, price and cost of spring steel, and environmental protection standards.
Why Choose Sino Special Metal?
Thank you for reading our article and we hope it can help you to have a better understanding of the anti-corrosion measures for spring steel in marine environment. If you are looking for spring steel suppliers and manufacturers online now, we would advise you to visit Sino Special Metal.
As a leading supplier of spring steel from Shanghai China, Sino Special Metal offers customers high-quality spring steel products such as 65Mn Spring Steel, 50CrV4 Spring Steel, 9260 Spring Steel, and SUP9 Spring Steel at a very competitive price.