Spring steel, as a superior alloy material, plays a pivotal role in modern industrial production. Given that the dimensional accuracy of spring steel directly influences the performance and service life of springs and other elastic components, it is imperative to strictly control the dimensional accuracy during the manufacturing and processing of spring steel. In this article, we’ll take a closer look at the control of dimensional accuracy in spring steel.
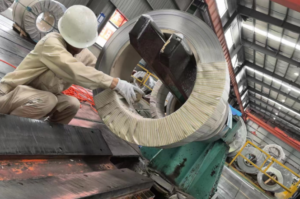
Control of Dimensional Accuracy in Spring Steel:
Firstly, in terms of material selection. Choosing the appropriate spring steel material is crucial to ensuring the performance and dimensional accuracy of springs. For instance, adding silicon to spring steel can significantly improve its elasticity and toughness. Incorporating vanadium, chromium, and other alloying elements can refine the microstructure of spring steel, enhancing its strength and hardness, which in turn affects the dimensional accuracy during manufacturing. Therefore, it is essential to ensure that the chemical composition of raw materials meets manufacturing requirements.
Secondly, focusing on processing techniques. The manufacturing precision of spring steel involves multiple aspects such as wire dimensions, shape, and surface quality. For instance, multiple cold drawing processes can enhance the dimensional accuracy, mechanical properties, and surface quality of spring steel, including tensile strength and elasticity. Additionally, cold drawing can reduce the size of spring steel, catering to the demand for various dimensional accuracies.
Thirdly, considering heat treatment processes. Heat treatment, a method of altering the internal structure of metallic materials through heating and cooling, significantly affects the dimensions and shape of spring steel, thereby influencing its precision. For example, quenching treatment significantly alters the crystal structure, grain size, and corresponding hardness of steel, enhancing the dimensional accuracy of spring steel.
Furthermore, emphasis on inspection and adjustment. By utilizing high-precision measurement tools to inspect processed spring steel materials, potential issues in dimensional accuracy can be promptly identified and adjusted accordingly. Common adjustment methods include shearing, grinding, and compressing. For instance, grinding involves removing excess material from the ends of spring steel using a grinding wheel to achieve precise lengths when the dimensional accuracy fails to meet specified standards.
Summary
In summary, the dimensional accuracy of spring steel significantly impacts the performance of spring components, including elasticity, hardness, and fatigue resistance. To ensure spring steel exhibits exceptional characteristics, it is necessary to control aspects ranging from material selection, processing techniques, heat treatment processes, to inspection and adjustment. Only by diligently managing these aspects can we produce high-precision spring steel products that cater to the demands of various industries for high-accuracy products.
Why Choose Sino Special Metal?
Thank you for reading our article and we hope it can help you to have a better understanding of the control of dimensional accuracy in spring steel. If you are looking for suppliers and manufacturers of spring steel online now, we would advise you to visit Sino Special Metal.
As a leading supplier of spring steel from Shanghai China, Sino Special Metal offers customers high-quality spring steel products such as 65Mn Spring Steel, 50CrV4 Spring Steel, 9260 Spring Steel, and SUP9 Spring Steel at a very competitive price.