As essential tools for cutting and machining mechanical parts, cutting tools must possess high hardness, wear resistance, and heat resistance. High-speed steel (HSS), with its outstanding hardness, wear resistance, toughness, thermal stability, workability, and corrosion resistance, fulfills various application requirements, making it an ideal material for the production of cutting tools. In this article, we’ll take a closer look at the advantages of high-speed steel in the manufacture of cutting tools.
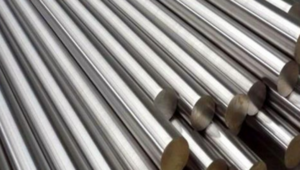
Advantages of High-Speed Steel in the Manufacture of Cutting Tools:
Firstly, in terms of hardness and wear resistance. High-speed steel contains a high level of carbon, which contributes to its exceptional hardness. Typically, the hardness of HSS ranges between HRC 67-69, enabling it to maintain sharpness during cutting and thereby extending tool life. Furthermore, the fine and uniformly distributed carbides in HSS ensure superior wear resistance, maintaining high cutting efficiency even under heavy loads.
Secondly, regarding thermal stability. HSS possesses excellent thermal stability, resisting softening and deformation in high-temperature environments. This enables it to maintain stability and durability over extended periods, making it suitable for high-temperature and high-speed cutting applications such as high-speed turning and milling.
Thirdly, in terms of toughness. The inclusion of manganese, a crucial alloying element, grants HSS good toughness and strength. Compared to some traditional steels, the higher manganese content in HSS imparts superior toughness to cutting tools, enabling them to maintain stable performance under high loads and impact conditions, reducing the risk of fracture and deformation.
Additionally, concerning corrosion resistance. The presence of chromium and molybdenum in HSS contributes to its corrosion resistance. Chromium reacts with oxidants to form a dense chromium oxide layer, while molybdenum resists common corrosive media like acids and alkalis. This feature preserves the surface finish and overall performance of the steel, further enhancing the tool’s longevity.
Furthermore, in terms of workability. HSS is highly workable, allowing for plastic deformation through heat treatment. This enables the production of cutting tools with complex structures and shapes, such as lathe tools, milling cutters, drill bits, broaches, gear cutters, and thread-cutting tools, to meet diverse cutting needs.
Conclusion
In conclusion, as a premium material for high-speed cutting tools, HSS excels in hardness, wear resistance, toughness, thermal stability, workability, and corrosion resistance, making it suitable for manufacturing various cutting tools. In industrial production, the application of HSS in cutting tools not only boosts productivity but also ensures extended tool life.
Why Choose Sino Special Metal?
Thank you for reading our article and we hope it can help you to have a better understanding of the advantages of high-speed steel in the manufacture of cutting tools. If you are looking for suppliers and manufacturers of high-speed steel, we would advise you to visit Sino Special Metal.
As a leading supplier of high-speed steel from Shanghai China, Sino Special Metal offers customers high-quality M2 High-Speed Steel, M35 High-Speed Steel, and M42 High-Speed Steel at a very competitive price.