High-speed steel, as a type of high-carbon alloy steel, boasts remarkable properties such as exceptional strength, hardness, and wear resistance, making it an indispensable material in the manufacturing of various cutting tools. Nevertheless, high-speed steel is not without drawbacks, and its relatively poor welding properties pose a significant challenge to its wider application. In this article, let’s take a closer look at the welding properties of high-speed steel.
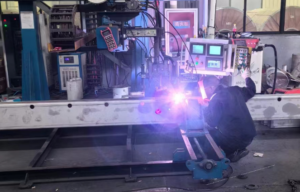
Analysis of the Welding Properties of High-Speed Steel:
The inferior welding properties of high-speed steel stem primarily from its chemical composition. The steel’s primary alloying elements—tungsten, molybdenum, vanadium, chromium, among others—collectively contribute to its outstanding mechanical and wear characteristics. Yet, these same elements also adversely affect its weldability. Notably, the high concentrations of tungsten and vanadium directly contribute to the decline in welding performance and a range of welding issues.
Specifically, the presence of these alloying elements in high-speed steel gives rise to several intricate problems during welding. Firstly, there is a heightened risk of hot cracking. The elevated levels of alloying elements in high-speed steel can cause fine hot cracks to form in the weld seam and heat-affected zone, ultimately leading to brittle fracture due to insufficient weld toughness. Secondly, there is a change in carbide distribution. During welding, the carbides within high-speed steel can fracture and disperse into the weld joint due to uneven heating, thereby reducing the hardness of the welded joint.
However, the welding challenges posed by high-speed steel are not insurmountable. In terms of welding materials, selecting electrodes or wires with lower tungsten and vanadium content can enhance the weldability of high-speed steel. Additionally, meticulous control over preheating temperature, welding temperature, and welding speed during the welding process can mitigate stress concentrations and subsequent weld distortion. Furthermore, adopting welding methods such as argon arc welding with a short arc length during welding can help prevent the formation of fine pores in the weld zone.
It is crucial to note that welding high-speed steel necessitates specialized skills and experience. Professional welders must develop detailed welding process plans tailored to specific grades of high-speed steel and welding requirements. Moreover, to ensure compliance with specific requirements, welders typically conduct rigorous post-weld inspections, a complex procedure that further restricts the widespread application of high-speed steel.
Conclusion
In conclusion, despite its widespread use in fields such as machinery manufacturing, aerospace, and automotive processing due to its superior properties, high-speed steel’s high alloy content negatively impacts its welding performance. In practical applications, selecting appropriate welding methods based on specific operating conditions and requirements is essential to enhancing the welding properties of high-speed steel.
Why Choose Sino Special Metal?
Thank you for reading our article and we hope it can help you to have a better understanding of the welding properties of high-speed steel. If you are looking for high-speed steel suppliers and manufacturers, we would advise you to visit Sino Special Metal.
As a leading supplier of high-speed steel from Shanghai China, Sino Special Metal offers customers high-quality M2 High-Speed Steel, M35 High-Speed Steel, and M42 High-Speed Steel at a very competitive price.