In our daily life, H13 and A2 tool steel are two very widely used materials, and they play a vital role in many industrial fields. In this article, we will analyze in detail the characteristics, chemical composition, and application scenarios of these two tool steels, H13 and A2, so that readers can have a deeper understanding of the differences between them.
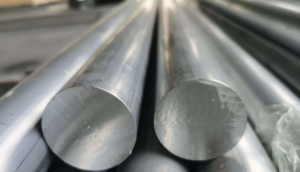
What is the difference between H13 and A2 tool steel?
1. Characteristics and applications of H13 tool steel
H13, also known as 4Cr5MoSiV1, is a high-alloy hot work die steel. It is known for its excellent high temperature toughness, wear resistance, oxidation resistance and thermal fatigue resistance. The excellent performance of H13 is mainly due to its unique chemical composition, which includes appropriate amounts of carbon, silicon, chromium, molybdenum, vanadium and other elements. The combination of these elements allows H13 to maintain high hardness and strength at high temperatures, ensuring the stability and durability of the mold at high temperatures.
The supply state of H13 is generally annealed, and the hardness usually does not exceed 235HBS. However, after proper heat treatment, the hardness of H13 can be significantly improved to meet the manufacturing needs of various complex molds. Due to its excellent performance, H13 is widely used in aluminum alloy die-casting molds, hot extrusion molds, hot forging molds, plastic molds and other fields.
2. Characteristics and applications of A2 tool steel
A2 tool steel, also known as DIN 1.2363, is a high carbon, high chromium, molybdenum and vanadium alloy tool steel. It is prized for its high hardness, excellent wear resistance and good toughness. The chemical composition of A2 steel contains a large amount of carbon and chromium, which allows it to form a high-hardness martensite structure after quenching, thereby providing excellent wear resistance. At the same time, the addition of molybdenum and vanadium also improves the toughness and impact resistance of A2 steel.
After proper heat treatment, the hardness of A2 steel can reach 57~62HRC, which makes it an ideal material for manufacturing high-load, high-precision molds. In addition, A2 steel also has good air-quenching performance and dimensional stability, which allows it to maintain a low deformation rate during the mold manufacturing process. Therefore, A2 steel is widely used in blanking dies, cold forming dies, cold drawing dies, wire cutting dies, thread rolling dies, crimping dies, plastic forming dies and other fields.
3. Comparison between H13 and A2 tool steel
When comparing H13 and A2 tool steels, we can find significant differences in several aspects. First, from a chemical composition perspective, H13 contains higher levels of carbon and vanadium, while A2 contains more chromium and molybdenum. This gives H13 better stability and wear resistance at high temperatures, while A2 has higher hardness and better toughness.
Secondly, from the perspective of application scenarios, H13 is mainly suitable for mold manufacturing in high-temperature environments, such as aluminum alloy die-casting molds, hot extrusion molds, etc. A2 is more suitable for the manufacturing of cold work molds and high-precision molds, such as blanking dies, cold work forming dies, etc. In addition, A2 is often used in mold manufacturing that requires high precision due to its good dimensional stability.
Finally, from the perspective of heat treatment process, both H13 and A2 need to undergo appropriate heat treatment to achieve optimal performance. However, due to their different chemical compositions and performance characteristics, the heat treatment process will also vary. When selecting a heat treatment process, comprehensive considerations need to be made based on specific material properties and application scenarios.
Conclusion
To sum up, there are significant differences between H13 and A2 tool steels in terms of chemical composition, performance characteristics, and application scenarios. When choosing which material to use, specific needs and conditions need to be considered.
Thank you for reading our article and we hope it can help you to have a better understanding of the difference between H13 and A2 tool steel. If you are looking for H13 and A2 tool steel suppliers and manufacturers online now, we would advise you to visit Sino Special Metal. As a leading supplier of tool steel from Shanghai China, Sino Special Metal offers customers high-quality tool steel products at a very competitive price.