SAE-AISI A2 Tool Steel (T30102) Air-Hardening Steel
A2 Tool Steel is an air-hardening, medium-alloy tool steel known for its good toughness and moderate wear resistance. It has a balanced composition, including around 1% carbon, 5% chromium, and small amounts of molybdenum and vanadium, which provides good hardness and stability during heat treatment. A2 is commonly used in applications that require high precision and durability, offering a good balance between wear resistance and impact toughness.
Please inquire now about your steel needs.
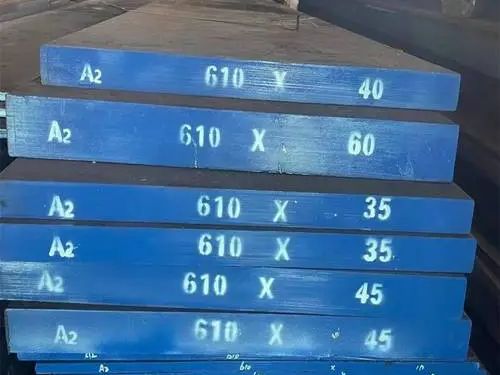
our A2 Tool Steel Supply: Available Forms and Sizes
Form | Thickness / Diameter | Width | Length |
---|---|---|---|
A2 Tool Steel Sheets | 1 mm – 20 mm | 300 mm – 1200 mm | 1000 mm – 3000 mm |
A2 Tool Steel Plates | 10 mm – 80 mm | 500 mm – 2000 mm | 1000 mm – 6000 mm |
A2 Tool Steel Round Bars | 10 mm – 400 mm diameter | – | 1000 mm – 6000 mm |
A2 Tool Steel Flat Bars | 5 mm – 80 mm thickness | 20 mm – 500 mm | 1000 mm – 6000 mm |
A2 Tool Steel Blocks | Customizable thickness | Customizable | Customizable |
A2 Tool Steel Square Bars | 10 mm – 200 mm | 10 mm – 200 mm | 1000 mm – 6000 mm |
Notes:
- Custom Sizes: Available upon request based on specific requirements.
- Tolerance: Dimensions may vary based on industry standards and client specifications.
- Heat Treatment: A2 Tool Steel can be supplied in annealed or pre-hardened conditions.
A2 Tool Steel material properties datenblatt as below:
chemical composition of A2 Tool Steel
Element | Content (%) |
---|---|
Carbon (C) | 0.95 – 1.05 |
Chromium (Cr) | 4.75 – 5.50 |
Molybdenum (Mo) | 0.90 – 1.40 |
Vanadium (V) | 0.15 – 0.50 |
Manganese (Mn) | 1.00 max |
Silicon (Si) | 0.50 max |
Phosphorus (P) | 0.03 max |
Sulfur (S) | 0.03 max |
Physical Properties of A2 Tool Steel
Physical Property | Value |
---|---|
Density | 7.7 g/cm³ |
Thermal Expansion | 11.7 x 10⁻⁶ /°C (20-100°C) |
Thermal Conductivity | 24.5 W/m·K at 20°C |
Specific Heat Capacity | 460 J/kg·K |
Electrical Resistivity | 0.70 x 10⁻⁶ Ω·m |
Melting Point | 1420 – 1460°C |
Mechanical Properties of A2 Tool Steel
Mechanical Property | Value |
---|---|
Hardness (Rockwell) | 57 – 62 HRC (after heat treatment) |
Tensile Strength | Approximately 1,930 MPa (depends on heat treatment) |
Yield Strength | Approximately 1,450 MPa |
Impact Toughness | Moderate (better than high-carbon tool steels) |
Modulus of Elasticity | 210 GPa |
Elongation at Break | 8 – 10% (varies with treatment) |
Applications of a2 Tool Steel:
- Punches and Dies: Ideal for precision tooling requiring toughness.
- Blanking Tools: Suitable for high-impact blanking and forming.
- Shear Blades: Effective for shearing applications due to its wear resistance.
- Molds and Injection Dies: Used in molds for plastic and rubber.
- Cutting Tools: Reliable for blades, knives, and trimming tools.
Different Designations for a2 Tool Steel:
Standard | Designation |
---|---|
UNS | T30102 |
AISI/SAE | A2 |
DIN | 1.2363 |
JIS | SKD12 |
ISO | X100CrMoV5 |
BS | BA2 |
EN | X100CrMoV5-1 |
Processing and heat treatment of A2 tool steel:
Forging
A2 Tool Steel should be slowly heated to 700°C, then quickly brought up to 1050-1100°C. Work should be performed below 900°C to avoid overheating. If necessary, the steel can be reheated to maintain optimal forging temperature. After forging, allow the steel to cool slowly.
Annealing
Annealing is performed by heating the A2 steel to 840-850°C, followed by soaking at this temperature and then cooling at a rate not exceeding 20°C per hour until reaching room temperature. This process will yield a maximum hardness of approximately 215 HB.
Stress Relieving
After heavy grinding or machining, it is recommended to stress relieve A2 Tool Steel to minimize the risk of warping or cracking during subsequent heat treatment. This is done by heating slowly to 670-700°C, soaking for two hours per 25 mm of thickness, then allowing it to cool in air.
Hardening
A2 Tool Steel should be preheated thoroughly to 600-700°C, then rapidly heated to the final hardening temperature of 950-980°C, ensuring uniform heating. After reaching the target temperature, the steel should be quenched in oil or air, depending on the desired properties.
Tempering
Temper A2 Tool Steel immediately after hardening. It should be reheated at intervals of 5 minutes per millimeter of thickness and tempered two to three times. For optimal toughness, tempering should be performed at 200°C or higher, which achieves a balance between hardness and toughness. For enhanced toughness, tempering at 350°C is recommended.
Contact us now! Free sample waiting for you.
Tel: +86-13012867759
Email: [email protected]
Tel: +86-021-54725826
Fax: +86-021-54717930
A2 tool steel is a versatile, air-hardening tool steel commonly used in the manufacturing of dies, punches, and cutting tools. It belongs to the A-grade tool steels, which are characterized by their high hardness, excellent wear resistance, and moderate toughness. A2 is typically hardened at moderate temperatures and has a good balance of properties, making it a popular choice in various industries.
Yes, A2 tool steel is an excellent choice for knives, especially those used for heavy-duty tasks like chopping or batoning. It provides a good balance of edge retention, toughness, and corrosion resistance compared to other tool steels. While it is not stainless, its moderate chromium content offers some resistance to rust. A2 knives require regular maintenance, such as oiling, to prevent corrosion.
A2 is part of the ASTM A681 specification for tool steels, which defines its chemical composition and properties. It contains approximately:
- 1.0% carbon for hardness,
- 5.0% chromium for wear resistance,
- 1.0% molybdenum, and
- 0.2% vanadium for toughness.
A2 is categorized as an air-hardening steel, meaning it hardens without the need for quenching in oil or water, reducing the risk of cracking during heat treatment.
The choice between A2 and D2 depends on the application:
- Toughness: A2 is tougher than D2, making it better for impact-heavy tasks.
- Edge Retention: D2 has superior edge retention due to its higher carbon and chromium content.
- Wear Resistance: D2 outperforms A2 in wear resistance, ideal for cutting tasks.
- Ease of Sharpening: A2 is easier to sharpen than D2.
- Corrosion Resistance: D2 has better corrosion resistance due to its semi-stainless composition.
For knives, A2 is preferred for durability, while D2 is chosen for long-lasting sharpness.
The “strongest” tool steel depends on the definition of strength:
- Hardness and Wear Resistance: Steels like M2 and D2 excel in these areas.
- Toughness: Steels like A2 and H13 are better for impact resistance.
- Overall Balance: A2 is often considered one of the strongest when combining toughness, wear resistance, and hardness.
A2 tool steel is equivalent to several international grades, such as:
- DIN 1.2363 in Europe,
- JIS SKD12 in Japan,
- BOHLER K245 as a branded equivalent.
These grades share similar chemical compositions and properties, suitable for tools requiring toughness and wear resistance.