SAE-AISI H13 Tool Steel (T20813) Chromium Hot-Work Steel
H13 Tool Steel is a chromium-molybdenum hot-work tool steel known for its excellent toughness, high wear resistance, and ability to withstand high temperatures. It has a balanced composition of chromium, molybdenum, and vanadium, providing it with good thermal conductivity and high resistance to thermal fatigue, making it ideal for hot-work applications.
Please inquire now about your steel needs.
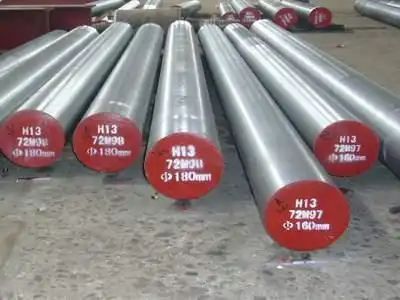
our H13 Tool Steel Supply: Available Forms and Sizes
Form | Thickness / Diameter | Width | Length |
---|---|---|---|
H13 Tool Steel Sheets | 1 mm – 20 mm | 300 mm – 1200 mm | 1000 mm – 3000 mm |
H13 Tool Steel Plates | 10 mm – 100 mm | 500 mm – 2000 mm | 1000 mm – 6000 mm |
H13 Tool Steel Round Bars | 10 mm – 500 mm diameter | – | 1000 mm – 6000 mm |
H13 Tool Steel Flat Bars | 5 mm – 80 mm thickness | 20 mm – 500 mm | 1000 mm – 6000 mm |
H13 Tool Steel Blocks | Customizable thickness | Customizable | Customizable |
H13 Tool Steel Square Bars | 10 mm – 200 mm | 10 mm – 200 mm | 1000 mm – 6000 mm |
Notes:
- Custom Sizes: Available upon request based on specific requirements.
- Tolerance: Dimensions may vary according to industry standards and client specifications.
- Heat Treatment: H13 Tool Steel can be supplied in annealed or pre-hardened conditions.
H13 Tool Steel material properties datenblatt as below:
chemical composition of H13 Tool Steel
Element | Content (%) |
---|---|
Carbon (C) | 0.32 – 0.45 |
Chromium (Cr) | 4.75 – 5.50 |
Molybdenum (Mo) | 1.10 – 1.75 |
Vanadium (V) | 0.80 – 1.20 |
Silicon (Si) | 0.80 – 1.20 |
Manganese (Mn) | 0.20 – 0.50 |
Phosphorus (P) | 0.03 max |
Sulfur (S) | 0.03 max |
Physical Properties of H13 Tool Steel
Physical Property | Value |
---|---|
Density | 7.80 g/cm³ |
Thermal Expansion | 11.0 x 10⁻⁶ /°C (20-100°C) |
Thermal Conductivity | 28.6 W/m·K at 20°C |
Specific Heat Capacity | 460 J/kg·K |
Electrical Resistivity | 0.55 x 10⁻⁶ Ω·m |
Melting Point | 1427°C |
Mechanical Properties of H13 Tool Steel
Mechanical Property | Value |
---|---|
Hardness (Rockwell) | 48 – 52 HRC (after heat treatment) |
Tensile Strength | Approximately 1,450 MPa |
Yield Strength | Approximately 1,200 MPa |
Modulus of Elasticity | 210 GPa |
Impact Toughness | High (suitable for hot-work applications) |
Elongation at Break | 10 – 15% (varies with treatment) |
Applications of H13 Tool Steel:
- Die Casting Dies: Suitable for molds exposed to high temperatures.
- Extrusion Dies: Ideal for shaping metals under intense heat.
- Forging Dies: Used in high-impact, high-temperature forging processes.
- Plastic Molds: Effective for plastic injection molds due to thermal stability.
- Hot Shear Blades: Withstands high heat during cutting operations.
Different Designations for H13 Tool Steel:
Standard | Designation |
---|---|
UNS | T20813 |
AISI/SAE | H13 |
DIN | 1.2344 |
JIS | SKD61 |
ISO | X40CrMoV5-1 |
BS | BH13 |
EN | X40CrMoV5-1 |
Fabrication and Heat Treatment of H13 Tool Steel:
Fabrication:
- Machining: H13 is relatively difficult to machine due to its high hardness, but it can be machined in its annealed state. Carbide-tipped tools are often recommended for better tool life.
- Grinding: H13 can be ground to precise dimensions after hardening, commonly used for final finishing.
- Welding: Welding H13 requires preheating to avoid cracking and post-weld heat treatment to restore hardness and toughness.
Heat Treatment:
Annealing:
- Heat slowly to 840-860°C, hold for a uniform soak, then cool at a rate not exceeding 10°C per hour down to 600°C. This process produces a maximum hardness of 229 HB (Brinell Hardness).
Stress Relieving:
- To relieve machining-induced stress, heat to 600-650°C, hold for 1-2 hours, then cool in air. This process minimizes distortion in further heat treatments.
Hardening:
- Preheat H13 to 600-700°C, then raise to 1000-1030°C and hold until uniformly heated. Quench in still air, oil, or pressurized gas for large sections. Air cooling minimizes distortion.
Tempering:
- Temper immediately after hardening by heating to 500-650°C for desired hardness, holding for 2 hours, then air cooling. Typically, H13 is tempered 2-3 times to increase toughness and thermal stability.
Contact us now! Free sample waiting for you.
Tel: +86-13012867759
Email: [email protected]
Tel: +86-021-54725826
Fax: +86-021-54717930