M2 Tool Steel
M2 Tool Steel is a high-speed steel renowned for its excellent hardness, wear resistance, and toughness. It is part of the tungsten-molybdenum (W-Mo) high-speed steel family, providing exceptional cutting performance and durability, even under high temperatures. The high tungsten, molybdenum, chromium, and vanadium content in M2 contributes to its hardness, allowing it to retain a sharp edge for extended periods, making it ideal for cutting and machining applications.
Please inquire now about your steel needs.
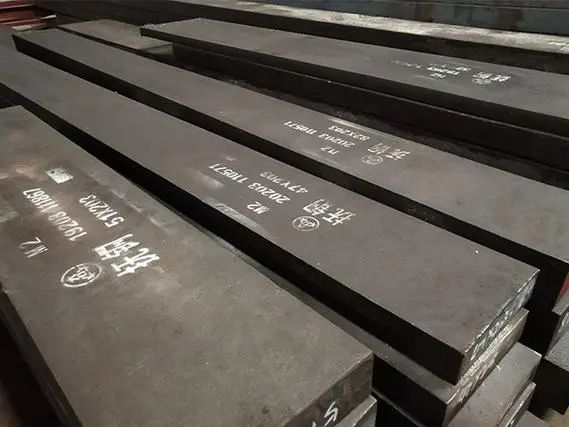
our M2 Tool Steel Supply: Available Forms and Sizes
Form | Thickness / Diameter | Width | Length |
---|---|---|---|
M2 Tool Steel Sheets | 1 mm – 20 mm | 300 mm – 1000 mm | 1000 mm – 3000 mm |
M2 Tool Steel Plates | 10 mm – 80 mm | 500 mm – 1200 mm | 1000 mm – 3000 mm |
M2 Tool Steel Round Bars | 5 mm – 300 mm diameter | N/A | 1000 mm – 6000 mm |
M2 Tool Steel Flat Bars | 3 mm – 50 mm thickness | 20 mm – 400 mm | 1000 mm – 6000 mm |
M2 Tool Steel Square Bars | 10 mm – 200 mm | 10 mm – 200 mm | 1000 mm – 3000 mm |
M2 Tool Steel Blocks | Customizable thickness | Customizable | Customizable |
As a professional and trusted m2 tool steel supplier, Sino-Specialmetal ensures high-quality M2 Tool Steel with a wide range of customizable forms and sizes to meet industry standards and client needs. Our expertise and commitment to quality make us a reliable partner for tool steel supply. Let us know if you have additional specifications or custom requirements!
M2 Tool Steel material properties datenblatt as below:
chemical composition of M2 Tool Steel
Element | Content (%) |
---|---|
Carbon (C) | 0.78 – 0.88 |
Tungsten (W) | 5.50 – 6.75 |
Molybdenum (Mo) | 4.50 – 5.50 |
Vanadium (V) | 1.75 – 2.20 |
Chromium (Cr) | 3.75 – 4.50 |
Manganese (Mn) | 0.15 – 0.40 |
Silicon (Si) | 0.20 – 0.45 |
Phosphorus (P) | 0.03 max |
Sulfur (S) | 0.03 max |
Physical Properties of M2 Tool Steel
Physical Property | Value |
---|---|
Density | 8.1 g/cm³ |
Thermal Expansion | 9.4 x 10⁻⁶ /°C (20-100°C) |
Thermal Conductivity | 23.0 W/m·K at 20°C |
Specific Heat Capacity | 420 J/kg·K |
Electrical Resistivity | 0.51 x 10⁻⁶ Ω·m |
Melting Point | 1,430 – 1,480°C |
Mechanical Properties of M2 Tool Steel
Mechanical Property | Value |
---|---|
Hardness (Rockwell) | 62 – 65 HRC (after heat treatment) |
Tensile Strength | Approximately 2,000 MPa |
Yield Strength | Approximately 1,500 MPa |
Modulus of Elasticity | 220 GPa |
Impact Toughness | Moderate (suitable for high-speed cutting) |
Compressive Strength | High (resists deformation under load) |
Applications of M2 Tool Steel:
- Drill Bits and End Mills: Ideal for high-speed drilling and milling due to its hardness and wear resistance.
- Lathe Tools and Cutting Blades: Retains sharp edges under high temperatures, suitable for precision cutting.
- Punches and Dies: Used in forming operations requiring impact resistance and durability.
- Reamers and Broaches: Maintains edge retention and accuracy for detailed machining tasks.
- Saw Blades: Suitable for high-speed saws where prolonged sharpness is required under heat.
M2 Tool Steel’s combination of hardness, wear resistance, and thermal stability makes it an optimal choice for cutting, machining, and forming applications in high-speed environments.
Different Designations for M2 Tool Steel:
Standard | Designation |
---|---|
UNS | T11302 |
AISI/SAE | M2 |
DIN | 1.3343 |
JIS | SKH51 |
ISO | HS6-5-2 |
BS | BM2 |
EN | HS6-5-2C |
Fabrication and Heat Treatment of M2 Tool Steel:
Fabrication
- Machining: M2 Tool Steel can be challenging to machine due to its high hardness and wear resistance. Machining is generally performed in the annealed (softened) state to reduce tool wear, with carbide-tipped tooling often recommended.
- Grinding: M2 Tool Steel requires precision grinding for finishing, especially after hardening. This is necessary to achieve exact dimensions and surface finishes.
- Welding: Due to its high carbon content, welding M2 is difficult and typically not recommended. If necessary, preheating and post-weld heat treatment are required to minimize cracking.
Heat Treatment
Annealing:
- Heat slowly to 850-900°C, hold for 1-2 hours, then cool in the furnace at a rate of 10°C per hour to about 600°C, followed by air cooling. This process will bring the steel to a maximum hardness of approximately 229 HB (Brinell Hardness).
Stress Relieving:
- To relieve machining-induced stress, M2 can be heated to 600-650°C, held for 1-2 hours, and then air-cooled. This process helps reduce the risk of warping during hardening.
Hardening:
- Preheat in stages to 450-500°C and then to 850-900°C. Afterward, rapidly heat to the final austenitizing temperature of 1,200-1,240°C. Once the material reaches uniform temperature, quench in oil, salt, or air for smaller sections. This yields maximum hardness.
Tempering:
- Temper immediately after hardening to achieve the desired hardness. M2 is commonly tempered at 540-600°C, depending on the required toughness and hardness balance. Multiple tempering cycles (2-3) are recommended for enhanced toughness and dimensional stability.
Key Considerations
Heat treatment processes like hardening and tempering are crucial in maximizing M2 Tool Steel’s hardness, wear resistance, and thermal stability, making it suitable for high-speed cutting and machining applications. Proper fabrication methods help maintain dimensional accuracy and prolong tool life.
Contact us now! Free sample waiting for you.
Tel: +86-13012867759
Email: [email protected]
Tel: +86-021-54725826
Fax: +86-021-54717930