Tool steel and die steel are both special steels widely used in industrial production. Although these two steels have some similarities, they have certain differences in material composition, performance characteristics, processing technology, cost price, and application scope. the difference. In this article, we discuss these 5 differences between tool steel and die steel.
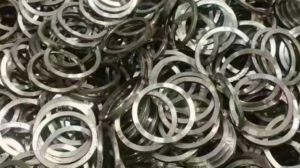
5 Differences between Tool Steel and Die Steel:
In terms of material composition, the alloying elements in tool steel are mostly tungsten, molybdenum and other elements, and the carbon content is generally between 0.6% and 1.5%. Mold steel contains rich alloying elements, such as chromium, nickel, molybdenum, tungsten, vanadium and other elements, and the carbon content is between 0.3% and 0.5%.
In terms of performance characteristics, tool steel has high hardness, can maintain high hardness and red hardness at high temperatures, as well as high wear resistance and appropriate toughness. In addition to its high strength, hardness, wear resistance, thermal stability and corrosion resistance, mold steel also has good processing properties.
In terms of processing technology, the service life of tool steel is closely related to the quality of heat treatment. When tool steel is heat treated, the pre-heat treatment is mostly spheroidizing annealing, and the final heat treatment is quenching plus medium-temperature tempering or high-temperature tempering to obtain good comprehensive mechanical properties. During the heat treatment of mold steel, especially during the quenching process, quality problems such as volume changes, shape warping, and distortion will occur, and it is difficult to accurately measure and control the temperature. The quenching temperature range of mold steel is wider.
In terms of cost price, generally speaking, the price of mold steel is relatively high. In the cost of mold production, material costs generally account for 10% to 20%, and mechanical processing, heat treatment, assembly and management costs account for more than 80%, and the special steel used to make molds has a certain impact on hardness, strength, wear resistance, toughness, etc. The performance requirements are high and the smelting and heat treatment processes are complex, resulting in relatively high production costs. The price of tool steel will also vary depending on the specific material, specifications and market demand. Especially some special tool steels, such as high-speed steel, may have higher prices due to difficult processing and high requirements.
In terms of application scope, tool steel is often used to manufacture various cutting tools, such as drill bits, milling cutters, taps, measuring tools, hammers, wrenches, etc. due to its high red hardness, good wear resistance, and high strength. Mold steel can effectively withstand factors such as pressure, heat, wear and corrosion under working conditions, and has high precision and stability. Mainly used to manufacture various types of molds, such as stamping molds, injection molds, die-casting molds, etc.
Conclusion
In short, although tool steel and die steel belong to the same category of special steel and both have high strength and high wear resistance, they have obvious differences in material composition, processing technology, cost price and application scope. Tool steel focuses more on manufacturing cutting tools and measuring tools, while mold steel is specially used to manufacture various molds and accessories. In practical applications, it needs to be selected according to specific working conditions and requirements.
Why Choose Sino Special Metal?
Thank you for reading our article and we hope it can help you to have a better understanding of the differences between tool steel and die steel. If you are looking for tool steel suppliers and manufacturers online now, we would advise you to visit Sino Special Metal.
As a leading supplier of tool steel from Shanghai China, Sino Special Metal offers customers high-quality tool steel products at a very competitive price.