Tool steel, as a crucial alloy material, experiences significant residual stress generation during the manufacturing process. The presence of these residual stresses can deteriorate the steel’s strength, fatigue resistance, and other properties, ultimately leading to potential fractures during use. Consequently, it is imperative to adopt suitable methods to reduce and eliminate the residual stress in tool steel.
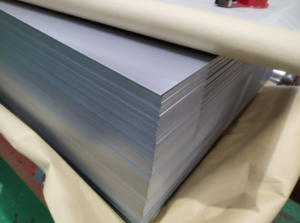
Residual Stress in Tool Steel and Its Elimination Methods:
Firstly, natural aging is a commonly employed method. In this approach, the workpiece is left outdoors, exposed to the elements like wind, sun, rain, and seasonal temperature fluctuations. These environmental factors repeatedly induce temperature stresses within the workpiece, causing the residual stresses to relax over time. Natural aging is typically suitable for eliminating stresses arising from casting, forging, machining, and welding processes.
Secondly, thermal aging is another effective method. This involves heating the tool steel slowly and uniformly from room temperature to approximately 550°C, holding it at this temperature for 4-8 hours, and then carefully controlling the cooling rate to below 150°C before removing it from the furnace. The thermal aging process demands rigorous temperature control; improper temperature management can significantly compromise its effectiveness, potentially introducing new temperature stresses similar to the original residual stresses, or even causing the workpiece to crack due to exceeding its stress limit.
Furthermore, mechanical treatment methods are also utilized. Mechanical stresses, such as those generated during cutting, stretching, or compression, can be addressed through mechanical stretching, which introduces additional deformations and stresses to counteract the existing residual stresses. Additionally, proper impact methods, like tapping, can effectively eliminate or reduce welding cracks, thereby eliminating residual stresses within the workpiece, particularly suitable for managing welding stresses.
Chemical aging methods are another option. Chemical reactions or corrosion can induce chemical stresses in steel. By employing chemical methods like immersion, coating, or even X-ray techniques, a stable compound layer can be formed on the workpiece’s surface, eliminating internal residual stresses. Notably, X-ray methods offer a non-destructive testing approach, preserving the integrity of the tool steel.
Lastly, surface treatment methods are highly effective in stress relief. Techniques like shot peening and polishing not only alter the surface shape and roughness of tool steel, redistributing stress and eliminating residual stresses, but also enhance the steel’s surface hardness, wear resistance, and corrosion resistance, ensuring a longer service life.
Conclusion
In conclusion, tool steel, with its exceptional properties, finds widespread applications in industries such as aerospace, automotive electronics, and engineering machinery. However, the internal residual stresses significantly limit its full potential. Therefore, selecting appropriate stress elimination methods provides crucial support for the extensive utilization of tool steel.
Why Choose Sino Special Metal?
Thank you for reading our article and we hope it can help you to have a better understanding of the residual stress in tool steel and its elimination methods. If you are looking for suppliers and manufacturers of tool steel, we would advise you to visit Sino Special Metal.
As a leading supplier of tool steel from Shanghai China, Sino Special Metal offers customers high-quality D2 Tool Steel(UNS T30402), A2 Tool Steel(UNS T30102), H13 Tool Steel(UNS T20813), M2 Tool Steel(UNS T11302) and O1 Tool Steel(UNS T31501) at a very competitive price.