Spring steel, as a high-performance alloy material, finds extensive applications in various industries such as engineering machinery, automobile manufacturing, electronic equipment, and more. With the continuous advancement of material technology, higher performance requirements are imposed on spring steel across these sectors. In the processing and manufacturing of spring steel, the adoption of essential surface strengthening techniques can significantly enhance its properties. In this article, let’s take a look at the surface strengthening techniques for spring steel.
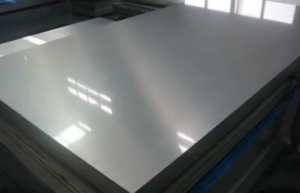
Surface Strengthening Techniques for Spring Steel:
Practically, surface strengthening treatments for spring steel not only eliminate residual stresses within the material but also bolster its surface wear resistance, corrosion resistance, and ultimately extend its service life. Several prevalent surface strengthening techniques include heat treatment, shot peening, and surface bluing.
Firstly, in terms of heat treatment strengthening techniques. Heat treatment, a common surface treatment process, encompasses protective atmosphere heat treatment, induction heating or protective atmosphere induction heating, and surface nitriding. Protective atmosphere heat treatment mitigates surface decarburization and oxidation, thereby improving the surface quality of spring steel. Induction heating or protective atmosphere induction heating, typically performed on wire prior to coil spring formation, facilitates grain refinement, reduces surface decarburization, and enhances the steel’s strength and toughness. Surface nitriding techniques, particularly low-temperature gas nitriding, markedly elevate the fatigue life of spring steel.
Secondly, regarding shot peening strengthening techniques. Spring steel shot peening processes encompass compound shot peening and stress shot peening. Compound shot peening, also known as multiple shot peening, achieves improved surface finish by utilizing shot particles of different diameters. Stress shot peening, renowned for its effective strengthening, can yield residual stress peaks up to 1500MPa in spring steel, leading to higher fatigue strength.
Additionally, surface bluing is another strengthening technique. Surface bluing involves heating steel or steel parts to an appropriate temperature in air, steam, or chemical solutions to form a blue oxide film on the surface. This process comprises degreasing, hot water rinsing, cold water rinsing, and bluing stages. Surface bluing not only enhances the wear resistance of spring steel but also achieves dual effects of corrosion prevention and aesthetics.
Conclusion
In conclusion, surface strengthening techniques play a pivotal role in enhancing the properties of spring steel during its processing and manufacturing. Heat treatment, shot peening, and surface bluing, each with their unique strengths, contribute significantly to the improvement of spring steel’s performance. Therefore, selecting the appropriate strengthening technique based on the specific application requirements and operating environment of the spring can ensure optimal performance.
Why Choose Sino Special Metal?
Thank you for reading our article and we hope it can help you to have a better understanding of the surface strengthening techniques for spring steel. If you are looking for suppliers and manufacturers of spring steel, we would advise you to visit Sino Special Metal.
As a leading supplier of spring steel from Shanghai China, Sino Special Metal offers customers high-quality 65Mn Spring Steel, 50CrV4 Spring Steel, 9260 Spring Steel, and SUP9 Spring Steel at a very competitive price.