Tool steel, as a crucial material in the metalworking industry, is renowned for its exceptional hardness, wear resistance, and ability to retain its cutting edge under heavy loads. Its chemical composition plays a pivotal role in imparting these desirable properties. In this article, we delve into the chemical composition of tool steel, highlighting the key alloying elements and their functions.
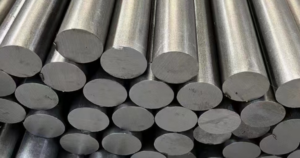
What is the chemical composition of tool steel?
Carbon (C)
Carbon is the primary alloying element in tool steel, responsible for imparting hardness and wear resistance. Higher carbon content results in increased hardness but can also reduce toughness. Tool steels typically contain carbon in the range of 0.6% to 1.5%, with specific grades tailored to achieve the desired balance between hardness and toughness.
Chromium (Cr)
Chromium is a key element in tool steel, enhancing hardness, wear resistance, and corrosion resistance. It also contributes to the steel’s heat resistance, allowing it to maintain its hardness at elevated temperatures. Chromium content in tool steel varies depending on the specific grade, but it is typically present in moderate to high percentages.
Molybdenum (Mo)
Molybdenum is an important alloying element in tool steel, known for its ability to improve hot hardness and toughness. It helps the steel retain its hardness and strength at high temperatures, enabling it to perform well in demanding applications. Molybdenum content in tool steel varies but is often included in moderate to high amounts.
Tungsten (W)
Tungsten is a critical component in high-speed tool steel grades, imparting extreme hardness and wear resistance. It is particularly effective in improving the steel’s cutting performance at high speeds. Tungsten content in tool steel is typically high in high-speed steel grades, but it may also be present in lower percentages in other tool steel types.
Vanadium (V)
Vanadium is an alloying element that is added to tool steel to enhance its wear resistance and toughness. It forms hard carbide particles within the steel matrix, improving its abrasion resistance. Vanadium is often included in moderate to low percentages in tool steel compositions.
Cobalt (Co)
Cobalt is an expensive but effective alloying element in tool steel, enhancing its hot hardness and wear resistance. It helps the steel maintain its hardness and cutting edge at elevated temperatures, improving its performance in high-speed cutting applications. Cobalt content in tool steel is typically low but can be increased in specific grades to enhance their high-temperature performance.
Other Alloying Elements
In addition to the aforementioned elements, tool steel compositions may also include other alloying elements such as nickel, manganese, silicon, phosphorus, and sulfur in smaller percentages. These elements can influence properties such as strength, ductility, and machinability, depending on their content and the overall steel composition.
Grade Classification
Tool steel grades are classified based on their chemical composition and intended applications. Common grade classifications include water-hardening steels, oil-hardening steels, air-hardening steels, and high-speed steels. Each grade has a unique chemical composition tailored to achieve specific properties and performance characteristics.
Conclusion
The chemical composition of tool steel plays a crucial role in determining its properties and performance. Key alloying elements such as carbon, chromium, molybdenum, tungsten, vanadium, and cobalt contribute to the steel’s hardness, wear resistance, heat resistance, and toughness.
Thank you for reading our article and we hope it can help you to have a better understanding of the chemical composition of tool steel. If you are looking for tool steel suppliers and manufacturers online now, we would advise you to visit Sino Special Metal.
As a leading supplier of tool steel from Shanghai China, Sino Special Metal offers customers high-quality tool steel products at a very competitive price.