D2 tool steel, a high-performance material widely utilized in various demanding industrial applications, stands out for its exceptional durability, wear resistance, and high compressive strength. In this article, we will delve into the composition of D2 tool steel, highlighting its key alloying elements and the roles they play in imparting its unparalleled properties.
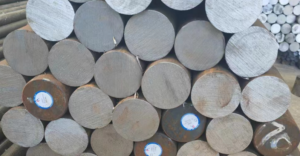
What is the composition of D2 tool steel?
Carbon (C)
The backbone of D2 tool steel’s exceptional hardness and wear resistance is its high carbon content. Carbon, being the primary hardening element, is present in D2 in a significant percentage, typically ranging from 1.40% to 1.60%. This high carbon content ensures that the steel achieves a high degree of hardness, making it suitable for applications that require extended durability and resistance to abrasion.
Chromium (Cr)
Chromium is another crucial element in D2 tool steel, contributing to its high wear resistance and corrosion resistance. It forms hard and stable carbides within the steel matrix, improving its abrasion resistance and durability. The chromium content in D2 tool steel is typically around 11.50% to 13.00%, ensuring a balance between hardness and toughness.
Molybdenum (Mo)
Molybdenum is an important alloying element in D2 tool steel, enhancing its hot hardness and toughness. It helps the steel retain its hardness and strength at elevated temperatures, enabling it to perform well in hot working applications. The molybdenum content in D2 tool steel is typically around 0.70% to 1.20%, contributing to its excellent hot hardness.
Vanadium (V)
Vanadium is an alloying element that is added to D2 tool steel to enhance its wear resistance and toughness. It forms hard carbide particles within the steel matrix, improving its abrasion resistance. The vanadium content in D2 tool steel is typically around 0.20% to 0.50%, playing a crucial role in imparting its exceptional durability.
Other Alloying Elements
In addition to the aforementioned elements, D2 tool steel may also contain other alloying elements in smaller percentages, such as manganese, silicon, phosphorus, and sulfur. These elements are added to further refine the steel’s properties, improving its machinability, toughness, and overall performance.
Heat Treatment
The composition of D2 tool steel, along with its heat treatment process, determines its final properties. Heat treatment involves heating the steel to a specific temperature and then cooling it at a controlled rate to alter its microstructure and enhance its properties. For D2 tool steel, a typical heat treatment process involves austenitizing the steel at a high temperature, followed by quenching in oil or water to achieve a high degree of hardness. Subsequent tempering at a lower temperature reduces the brittleness and improves the toughness of the steel.
Applications
D2 tool steel’s unique composition and properties make it an ideal choice for various demanding applications. It is widely used in the manufacturing of cutting tools, dies, punches, and other tools that require high wear resistance and durability. Its high compressive strength and toughness also make it suitable for applications that involve heavy loads and impact.
Conclusion
In conclusion, D2 tool steel’s composition, consisting of high carbon, chromium, molybdenum, and other alloying elements, imparts it with exceptional properties such as hardness, wear resistance, and high compressive strength. Its unique composition and heat treatment process enable it to perform well in various demanding industrial applications, making it a preferred choice for manufacturers and toolmakers.
Thank you for reading our article and we hope it can help you to have a better understanding of the composition of D2 tool steel. If you are looking for D2 tool steel suppliers and manufacturers online now, we would advise you to visit Sino Special Metal.
As a leading supplier of tool steel from Shanghai China, Sino Special Metal offers customers high-quality D2 tool steel at a very competitive price.