Conventional high speed steel (HSS) metallurgy stands as a cornerstone of industrial progress. The intricate art of crafting this alloy, a blend of iron, carbon, and various alloying elements, has evolved over centuries, resulting in a material that is prized for its exceptional hardness, wear resistance, and cutting capabilities. This article delves into the nuances of conventional high speed steel metallurgy, outlining its composition, manufacturing processes, properties, applications, and the role it plays in the modern industrial landscape.
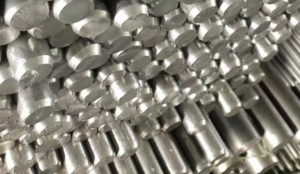
Conventional High Speed Steel Metallurgy
Composition and Alloying Elements
The fundamental composition of conventional HSS revolves around iron, the backbone of the alloy. Carbon, an essential constituent, is added to enhance the hardness and wear resistance of the steel. However, the true magic lies in the addition of alloying elements, such as tungsten (W), molybdenum (Mo), cobalt (Co), chromium (Cr), and vanadium (V). These elements, in varying proportions, determine the specific properties and performance characteristics of the steel.
Tungsten, for instance, is a critical addition that significantly increases the hardness and hot hardness of the steel. Molybdenum, on the other hand, enhances the red hardness, or the ability to retain hardness at elevated temperatures, making it ideal for high-speed cutting applications. Cobalt, known for its excellent carbide stability, further improves the wear resistance of the steel. Chromium, in addition to its corrosion resistance properties, also contributes to the overall hardness of the alloy. Lastly, vanadium, in the form of carbides, provides localized hardness enhancement, critical for cutting edges.
Manufacturing Processes
The manufacture of conventional high speed steel (HSS) involves a series of carefully controlled steps, starting with the selection and blending of raw materials. The alloying elements are precisely weighed and mixed with iron and carbon to achieve the desired chemical composition. This mixture is then melted in a furnace at high temperatures, allowing the elements to homogenize and form a liquid alloy.
Once melted, the alloy is poured into ingots, which are then subjected to various heat treatments to alter its microstructure and properties. This includes austenitization, where the alloy is heated to a critical temperature to transform its microstructure, and quenching, a rapid cooling process that locks in the desired properties. Subsequent tempering steps further refine the microstructure, improving toughness and reducing brittleness.
After heat treatment, the ingots are rolled or forged into billets or bars, which are then machined into the final shapes and sizes required for various applications. The final stage involves precision grinding and polishing to achieve the desired surface finish and dimensional accuracy.
Properties and Applications
The unique composition and manufacturing processes of conventional high speed steel (HSS) result in a material with exceptional properties. Its high hardness and wear resistance make it ideal for use in cutting tools, such as drill bits, taps, and milling cutters. The ability to retain hardness at elevated temperatures allows HSS to perform effectively in high-speed machining operations, where tool temperatures can rise significantly.
In addition to cutting tools, conventional high speed steel (HSS) is also used in a variety of other applications where durability and wear resistance are paramount. This includes dies for metal forming, punches for stamping operations, and even in some instances as a wear-resistant coating for other materials.
The Role of Conventional High Speed Steel (HSS) in the Modern Industrial Landscape
In the rapidly evolving landscape of modern industrial materials, conventional high speed steel (HSS) continues to occupy a crucial position. Its unique properties and versatility have made it an indispensable tool in the arsenal of manufacturers and engineers. As manufacturing processes become more sophisticated and demanding, the need for high-performance cutting tools and wear-resistant components continues to grow.
Moreover, the ability to tailor the properties of HSS through the precise control of alloying elements and manufacturing processes offers a level of customization that is unparalleled in other materials. This flexibility allows manufacturers to optimize tool performance for specific applications, further enhancing the efficiency and productivity of modern industrial operations.
Conclusion
In conclusion, conventional high-speed steel metallurgy represents a blend of art and science, a testament to the ingenuity and dedication of metallurgists and material scientists.
Thank you for reading our article and we hope it can help you to have a better understanding of conventional high speed steel metallurgy. If you are looking for high-speed steel suppliers and manufacturers online now, we would advise you to visit Sino Special Metal.
As a leading supplier of high-speed steel from Shanghai, China, Sino Special Metal offers high-quality high-speed steel products at a very competitive price.