Tool steel, as a critical material in the manufacturing industry, is renowned for its exceptional hardness, wear resistance, and ability to retain its cutting edge under high temperatures. Its diverse grades are tailored to meet specific applications, ranging from precision cutting to heavy-duty forming operations. This article delves into the 6 primary grades of tool steel, highlighting their unique characteristics, and applications.
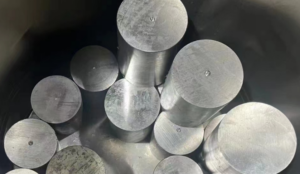
What are the 6 grades of tool steel?
6 Primary Grades of Tool Steel – 1. Water-Hardening Steel (Group O)
Water-hardening steel, also known as Group O steel, is the most basic type of tool steel. It derives its name from the quenching process, where the steel is cooled rapidly in water to achieve its desired hardness. This grade contains a relatively low carbon content, along with manganese and chromium, which contribute to its hardening capacity.
- Characteristics: Water-hardening steel is easy to machine in its unhardened state, but it tends to be brittle after hardening. It has good shock resistance but limited wear resistance.
- Applications: Due to its brittleness, water-hardening steel is typically used for making punches, dies, and other tools that require shock resistance but not extreme wear resistance.
- Processing: It is heat-treated by heating to a critical temperature, followed by rapid cooling in water.
6 Primary Grades of Tool Steel – 2. Air-Hardening Steel (Group A)
Air-hardening steel, or Group A steel, is a more advanced grade that can achieve high hardness levels without the need for water quenching. It contains a higher carbon content and alloying elements such as molybdenum and vanadium.
- Characteristics: This steel has excellent hardness and wear resistance, making it suitable for applications requiring long-lasting cutting edges. It is also more ductile than water-hardening steel.
- Applications: Air-hardening steel is commonly used for making cutting tools, punches, dies, and other precision tools.
- Processing: Heat treatment involves heating to a critical temperature and then allowing the steel to cool slowly in air.
6 Primary Grades of Tool Steel – 3. Oil-Hardening Steel (Group O-1)
Oil-hardening steel, belonging to the Group O-1 classification, is a versatile grade that offers a balance between hardness and toughness. It is quenched in oil, allowing for a slower cooling rate than water, which reduces the risk of cracking.
- Characteristics: Oil-hardening steel exhibits good wear resistance and toughness, making it a popular choice for tools that require both qualities.
- Applications: This steel is commonly used for making dies, punches, and other forming tools. It is also suitable for some cutting applications.
- Processing: Heat treatment typically involves heating to a critical temperature and then quenching in oil.
6 Primary Grades of Tool Steel – 4. Hot-Work Tool Steel (Group H)
Hot-work tool steel, or Group H steel, is specifically designed for applications involving high temperatures. It contains alloying elements such as chromium, molybdenum, and vanadium, which enhance its resistance to softening and wear at elevated temperatures.
- Characteristics: Hot-work tool steel has excellent thermal stability and resistance to softening, making it suitable for use in forging dies, extrusion dies, and other hot-working applications.
- Applications: This steel is commonly used in forging presses, extrusion machines, and other equipment that operates at high temperatures.
- Processing: Heat treatment includes austenitizing at a high temperature and then quenching in oil or water, depending on the specific alloy.
6 Primary Grades of Tool Steel – 5. Cold-Work Tool Steel (Group D)
Cold-work tool steel, or Group D steel, is used for applications involving cutting, shearing, or forming at room temperature or below. It is formulated to provide maximum wear resistance and hardness.
- Characteristics: Cold-work tool steel exhibits excellent hardness, wear resistance, and dimensional stability. It is often used in precision applications.
- Applications: This steel is commonly used for making cutting tools, punches, dies, and other precision tools that require high accuracy and durability.
- Processing: Heat treatment typically involves heating to a critical temperature and then quenching in oil or water, followed by tempering to achieve the desired hardness and toughness.
6 Primary Grades of Tool Steel – 6. High-Speed Steel (Group M)
High-speed steel, also known as Group M steel, is a specialized grade designed for cutting tools such as drill bits, taps, and end mills. It contains tungsten, molybdenum, cobalt, and other alloying elements that enhance its ability to retain hardness at high temperatures.
- Characteristics: High-speed steel has excellent cutting performance and can maintain its hardness and wear resistance at temperatures up to 600°C.
- Applications: This steel is used extensively in the manufacturing industry for cutting operations that require high cutting speeds and durability.
Conclusion
Thank you for reading our article and we hope it can help you to have a better understanding of the 6 primary grades of tool steel. If you are looking for tool steel suppliers and manufactuers online now, we would advise you to visit Sino Special Metal.
As a leading supplier of tool steel from Shanghai China, Sino Special Metal offers customers high-quality tool steel products at a very competitive price.